QC System
We have a rigorous quality inspection system.
Our inspectors are responsible for our products.
Our directors are responsible for Seallon's regulations and reputation.
Our sales managers are responsible for our customers.
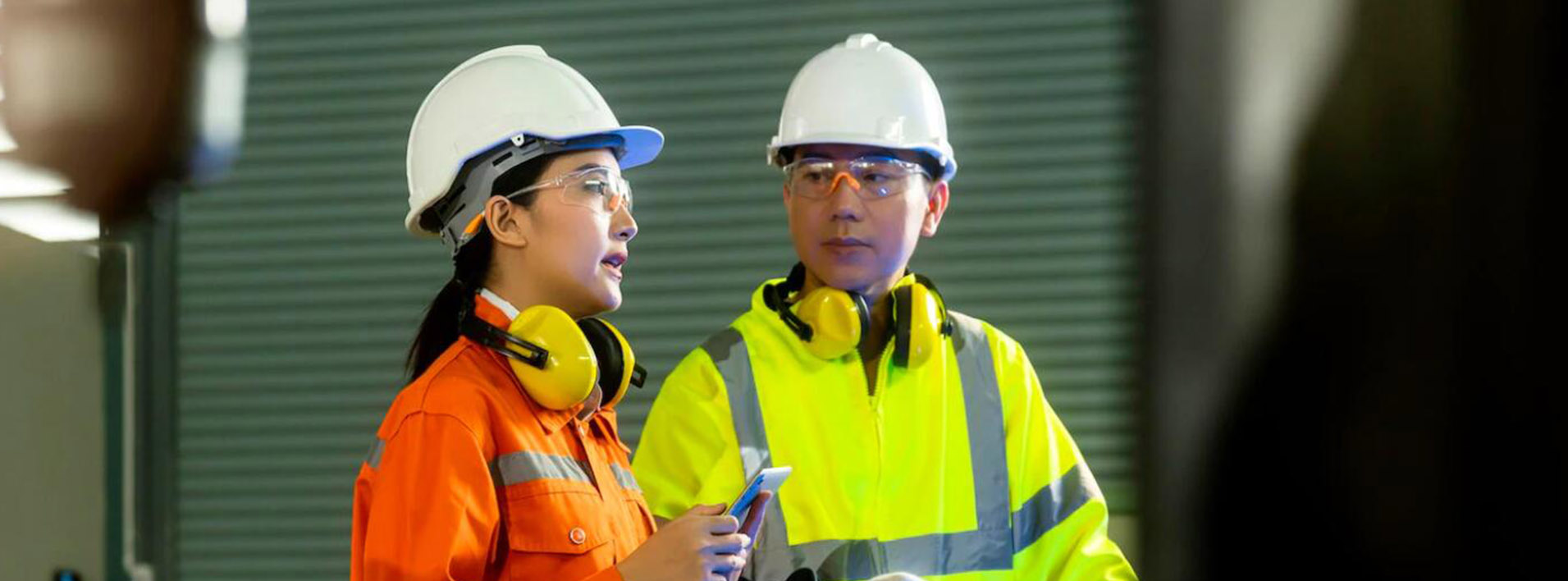
Only 4 Steps with Seallon
Ensure that, your order is completed and shipped accurately
1. Pre-sales consultation & technical confirmation 2. Production schedule 3. During production inspection 4. Pre-shipment inspection
Seallon's Quotation and Drawings
Necessary questions for technical confirmation
Confirm with your sales manager the specifications and other special requirements of the order as much as possible:
1. Working conditions of the valves and accessories (working medium, working pressure, working temperature, etc.);
2. The series model of the product (drive, connection, composition structure, material of main parts, etc.);
3. The standard and sizes of the product (F-F dimension, diameters, holes dimensions, sizes for actuators, etc.);
4. Delivery time, packing, trade terms, etc.;
5. Special requirements of the order.
Seallon`s Production & Delivery Plan ERP
Customers should know the progress of their orders
Seallon`s self-developed ERP system can realize efficient production management, optimize production processes, and reduce production costs.
1. Make detailed records of warehouse entry and exit operations in the system, clarify the capacity of each material(semi-finished product or product, etc);
2. The system can associate the company's sales order with the factory's production plan and disassembled production tasks. The completion of each production work order is updated in real time. Workshop management can check the progress of the production work order at any time and give timely feedback to the sales department.;
3. Through the system, production tasks are issued and queried clearly and quickly. Production workers can automatically report on a daily basis. The results of the report are approved by the workshop director or quality inspector. After the approval is passed, the production progress will be automatically updated.
First Product Inspection and Materials & Measurements Inspection
Detect and identify the problems in time, reduce the defective product rate, take effective improvement measures, and give feedback to customers
1. Check the appearance and material composition of the castings and accessories according to the order requirements and standards, and confirm the access to the processing link;
2. Count the quantity and confirm the batch and quantity of semi-finished products and finished products;
3. Make random sampling of semi-finished products and some finished products under each process according to the AQL calculation results;
4. Keep photos and video data taken in each process.
Varieties of Inspection Methods
We can be as professional as a third-party inspection company. In addition, we are responsible for the inspection results immediately and directly
Insights
Learn more about how Seallon can help and serve you
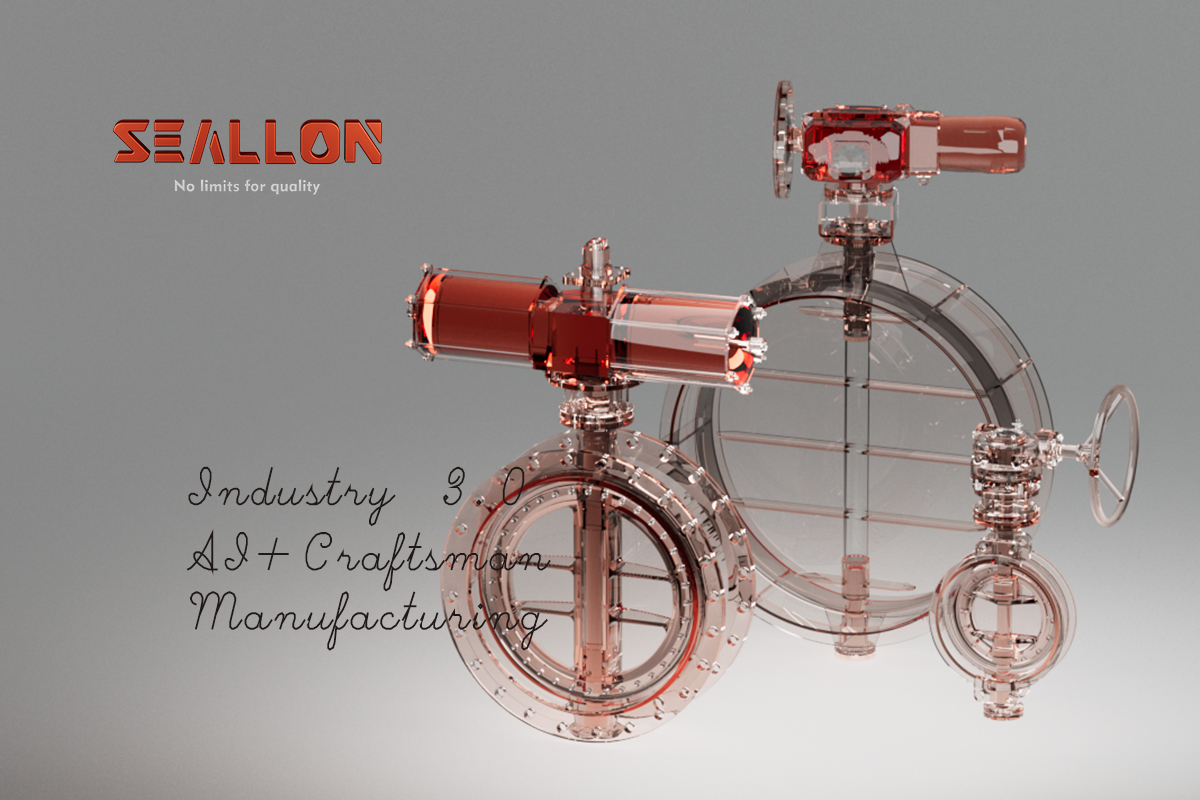
Company News
Follow the latest news, trends and shipping records of Seallon, to build a connection with us right now.
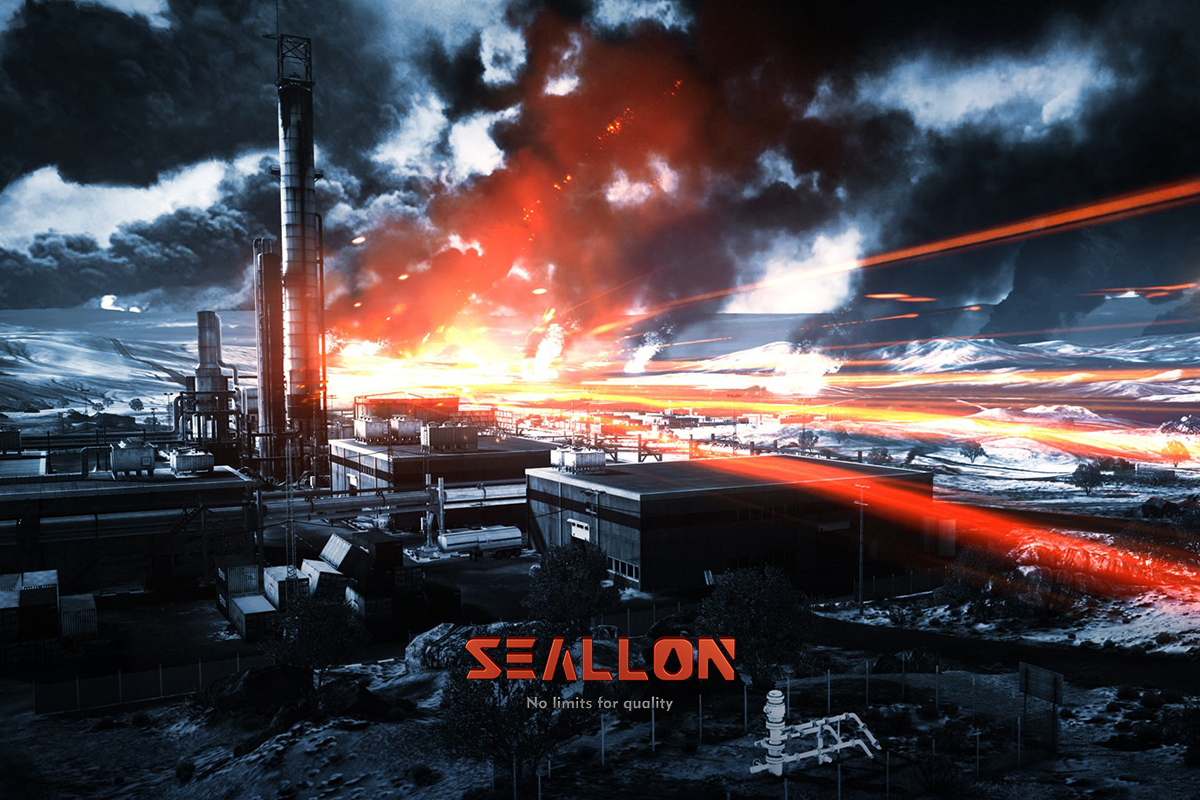
Classic Cases
Scan the real development and service results of Seallon, to provide reference for the upcoming cooperation.
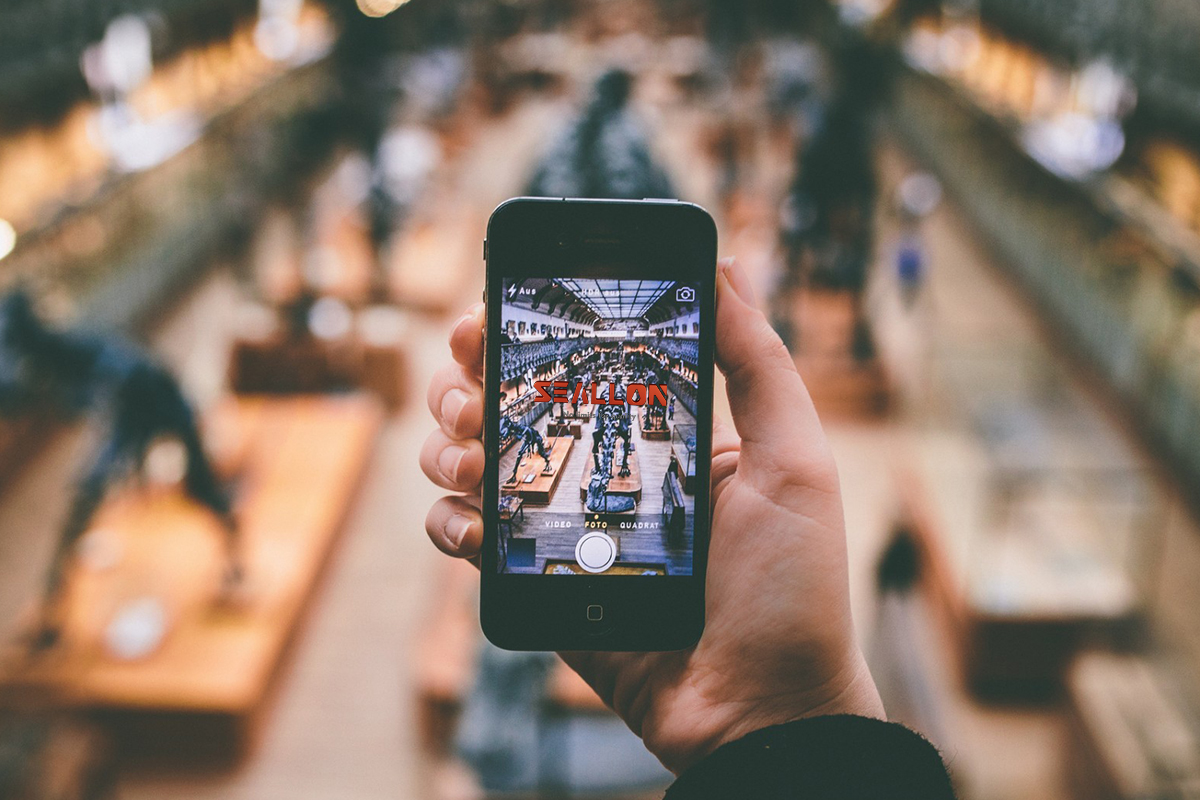
Videos
Enable to have a 5D understanding of Seallon and our products, gain both a qualified supplier and a wealth of knowledge.